
Лето 2003 года. Как-то неожиданно пришло решение, что уже пора, хотя бы с третьей попытки обзавестись собственным судном. Но для любого, даже спонтанного решения есть основания, иногда осознаваемые позже. Какие же основания были у меня.
Это давнишнее увлечение кораблестроением, начавшееся с покупкой моей мамой в 1966 году седьмого номера сборника "Катера и Яхты". Как помню, стоил он 1 рубль 11 копеек и был куплен в книжном киоске от книжного магазина "Судостроитель" на станции метро "Площадь мира".
Это и то, что получив образования судостроителя, хватило разума не оставаться работать постоянно в этой отрасли. Благодаря этому кораблестроение осталось моим увлечением на всю оставшуюся жизнь, а не каторгой за зарплату.
Это и занятия парусным спортом с 1972 года.
И чисто материальный довод. Возможность использовать в нерабочее время профессиональную столярную мастерскую площадью 2000 квадратных метра с полным комплектом оборудования, от банальных рейсмуса и фуганка до горячих прессов.
В клубе "Балтиец" к тому времени у меня уже было место, поэтому поиски подходящего под мои хотелки судна этим клубом и ограничились. Поиски были недолгими. Быстро нашел в продаже катер на основе спасательной шлюпки. Главное, что был алюминиевый корпус в достойном состоянии и рабочий двигатель, не требующий ремонта. Остальное меня не волновало. Несколько фото моего приобретения.

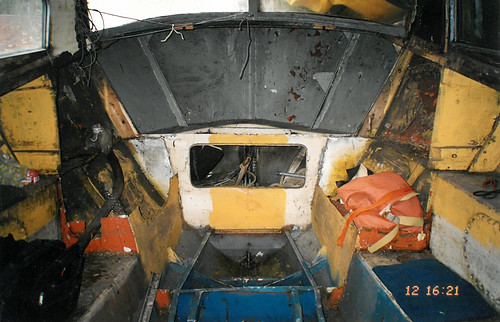



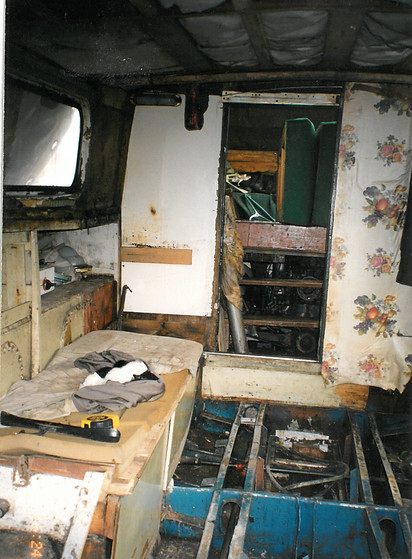
И так осень 2003 года, старт строительства.
В клубе полная очистка до голого корпуса с двигателем и валовой линией. Замеры.
Дома рисование в САПРе проекта.
И оценка имеющихся возможностей и ресурсов.
А ресурсы имелись материальные и не материальные.
Материальные:
1.Корпус спасательной шлюпки из АМГ размерениями 8,5х3 и полезной грузоподъемностью 55 чел или 4000кг, а точнее катер на базе этой шлюпки, с которого я снес все деревяшки предыдущего хозяина, ибо он с деревом не дружил, и оставленный на месте в шлюпке двигатель Д65 с реверс-редуктором и упорным подшипником, ибо с металлом и механизмами дружба была вполне обоюдной.
2.Место в Питерском клубе *Балтиец* с контейнером.
3. Судовой билет на этот катер, в котором было указано, что это парусно-моторное маломерное судно с площадью парусности 30 м2 и вместимостью 8 человек.
Нематериальные:
1. Желание и возможности произвести перестройку спасательной шлюпки в парусно-моторное судно в соответствии со своими взглядами на этот вопрос, сформированными за время хождения на яхтах типа Л6, Таурус, Картер30 и других начиная с 1972 года.
А взгляды эти, со временем переросшие в убеждения следующие:
- район эксплуатации - Нева, Ладога, Свирь, Онега, Балтика.
- вид эксплуатации - дальние плавания с экипажем 3-4 человека.
- рабочие места на судне должны быть максимально удобны и безопасны в пределах возможности такового в имеющихся размерениях.
Рабочие места это носовая и кормовая палубы - работа с якорными и швартовными концами, потопчины шириной не менее 450мм - свободный и безопасный проход по борту (леера обязательны), крыша рубки - свободная с небольшой погибью - работа с парусами, ходовая рубка - только полузакрытая, защищающая от ветра и дождя и со свободным проходом в кокпит. Камбуз с возможностью работать в полный рост, с двухконфорочной плитой и мойкой, и рабочим столом не менее 600х450.
Штурманский стол габаритов не менее 800х600 и с удобной седушкой.
Кокпит - универсальное место, и работа и отдых и просто времяпровождение, поэтому кроме удобства для этого самого времяпровождения хотелось бы банки кокпита использовать как резервные спальные места для кратковременного пересыпа.
Места отдыха - обязательно полноразмерные койки не менее 1900х600.
Места кратковременного пребывания - обеденный стол, ахтерпик и гальюн - жертвенные места в пользу двух первых. Кстати по опыту гальюн одно из самых редко посещаемых заведений на маломерном судне в дальнем длительном плавании.
В процессе работ фотографий не делал. Есть только фото до *ТОГО* и фотографии в первый, после семилетних трудов, год на воде.


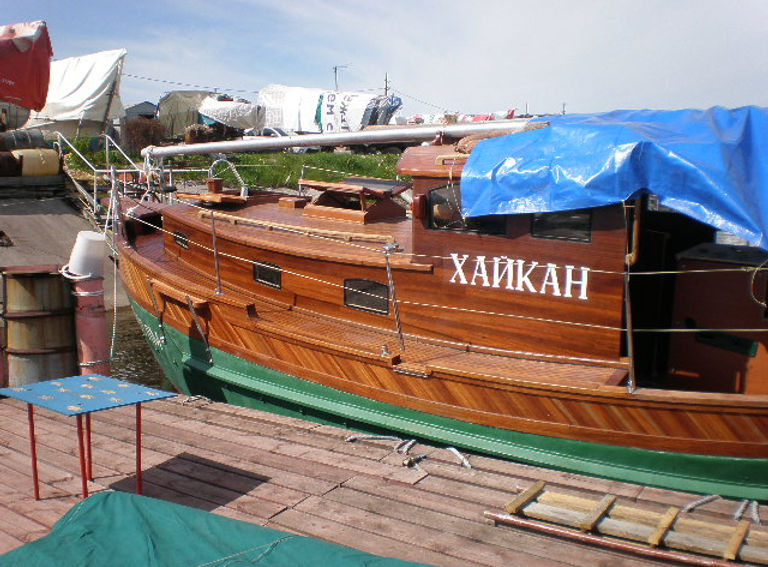
Получилось неплохо. Но визуально рубка из красного дерева выглядит тяжеловато, напрашивается светлый тон, например окраска в белый цвет.
Немного конструктива


Фотографий не делал, но учет трудозатрат вел. С 2003 года до момента спуска на воду в 2011 году. Результаты таковы.
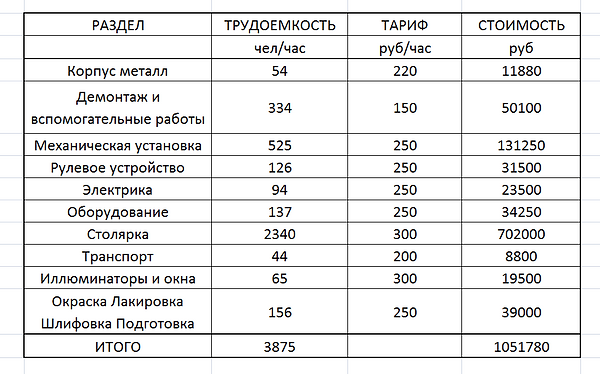
О материальном, точнее о материалах, примененных при строительстве.
*Я его слепила из того, что было...*. А было масса отходов дуба и красного дерева (макоре и кайя) в виде коротья длинной 350-450 мм и длинномерный обрез толщиной 5-12мм. Естественно все сделать из отходов не удалось, пришлось докупать. Расклад примерно такой - 70% из отходов и 30% деловой древесины.
Вообще конструктив определяется в основном технологическими возможностями изготовителя. Как уже говорил, у меня была возможность пользоваться неплохой профессиональной столярной мастерской, именно поэтому не стоял вопрос, из какого материала наращивать борт.И высота наращивания определялась длинной отходов.
Фанера использовалась марки ФСФ. Но в данном контексте марка фанеры не критична, ибо она нигде не открыта для внешнего атмосферного воздействия. На палубе и крыше рубки фанера использовалась в качестве подложки для укладки рейки из красного дерева (татаюбы) (тик по цене 350000р за м3 мне не потянуть) на сикафлекс.
По вопросу устойчивости дерева к атмосферным воздействиям (вода, влага, ультрафиолет) - всю облицовку из дерева ставить на сикафлекс или подобные герметики на слой толщиной не менее 2 мм с разбежкой между делянками не менее 5% от ширины делянки.
Сам я сделал ошибку - в силу финансовых затруднений облицовку стенок (комингсов) рубки выполнил на эпоксиде. За три месяца стоянки левым бортом точно на юг эпоксид не выдержал напряжений *гуляющей* древесины и частично расслоился, что привело к появлению водотечности. Впоследствии выполнил еще один слой облицовки дубовой рейкой на сикафлексе.

На фото можно увидеть кап над двигателем. Очень загромождает кокпит. Но вещь вынужденная и история его появления такова. Установленный двигатель Д65 довольно высок и спрятать его полностью под палубу кокпита не удавалось, получался кап высотой не менее 400мм. Такая высота на палубе несколько опасна, споткнуться о него очень просто. А на качке он может
выступить в роли *подножки.* Уж лучше сделать не ниже 800мм. Решил минимизировать недостатки от наличия капа путем максимального использования его объема. В верхней части капа разместил расходный топливный бак, расширительный бачок системы охлаждения, бензобак для пускового двигателя и отсек для хранения моторных инструментов. В моем случае размещение расходного топливного бака выше топливного насоса есть вещь обязательная и необходимая, ибо именно так расположен топливный бак на тракторах ЮМЗ с двигателем Д65. Знаю случаи, когда при заборе топлива ниже уровня топливного насоса, на волнении, особенно на крутой Онежской волне возникали перебои с подачей топлива. Что было причиной этого явления, то ли качка выявляла недостатки герметичности топливной системы, то ли давала себя знать способность солярки к пенообразованию - не выяснял. Но высокое расположение расходного топливного бака устраняет вероятность подобного явления.
Общее расположение понятно из фотографий, выполненных в походном, без лишнего рекламного лоска, состоянии.


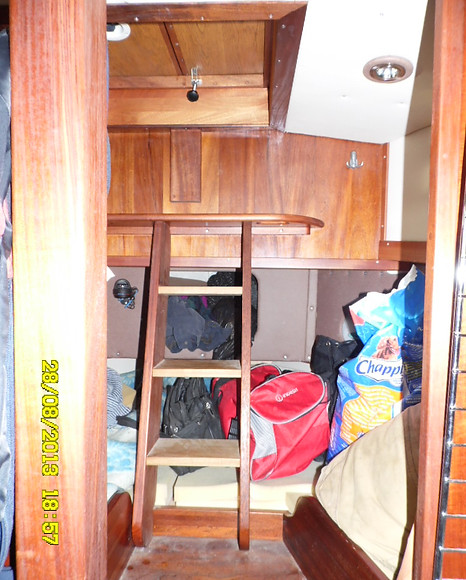
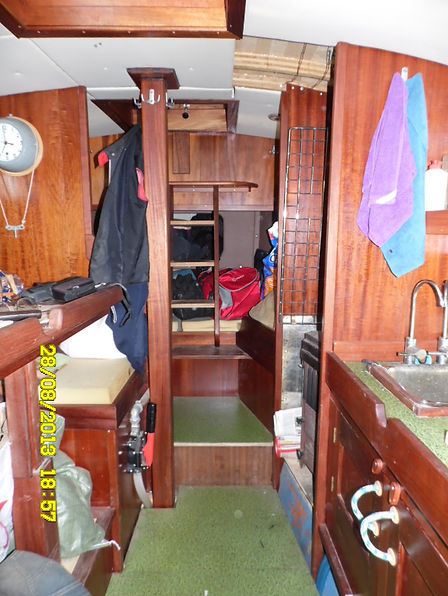


БОЛЕЕ ПОДРОБНО О КОНСТРУКТИВЕ. Наращивание борта.
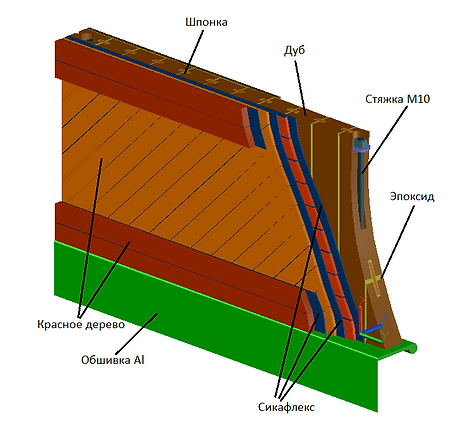

Борт с палубой.

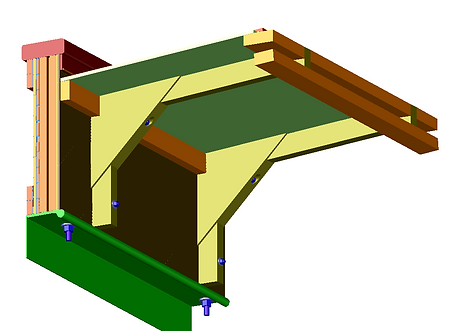
Борт, палуба и комингс рубки.
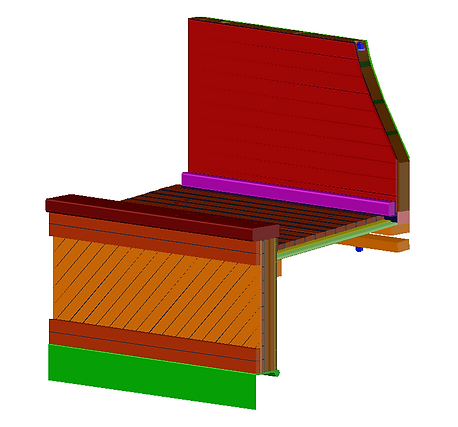

О КЛЕЯХ.
При строительстве использовалось четыри разновидности клеев и герметиков. Это эпоксидный компаунд К-153 с отвердителем ПЭПА, это клеи и герметики Sikaflex, это ПВА клей Беррит 303 и в очень небольшом объеме силиконовые бескислотные герметики различных производителей.
Залог надежности клеевых соединений - это соблюдение технологии, и не только в части правильного соотношения компонентов, но во всем остальном, как влажность, температура, время использования, метод нанесения, толщина клеевого слоя, давление запрессовки, время выдержки под давлением.
Все силовые элементы конструкции, в том числе криволинейные, были выполнены на эпоксидном компаунде К-153. Важно обеспечить небольшое давление запрессовки, при котором толщина клеевого слоя не менее 0,3-0,5 мм. Нет смысла оценивать давление в
кг/см2, ибо измерить его довольно трудно. Но использовать маячки соответствующей толщины весьма полезно. Но при наличии опыта и маячки оказываются лишними. В тоже время при склейке деталей из дуба иногда наблюдается нестабильность качественного результата. Поэтому стоит очень строго подойти к показателям влажности и температуры древесины и окружающей среды. И не доходить до фанатизма в части шероховатости склеиваемых поверхностей. Лучше поверхность из-под пильного диска, или из под цинубеля, но обязательно обеспыленная.
Эксплуатация судна показала, что эпоксид не может быть универсальным клеем. В некоторых ситуациях клеевое соединение постепенно разрушается. В частности стенки рубки первоначально были облицованы рейкой из дерева Ироко на эпоксиде. В гавани лодка стояла всегда носом на запад, то есть левый борт был обращен на юг. Видимо эпоксид не выдержал напряжений от *гуляющей* от перегрева древесины и отслоился. Как следствие появилась водотечность. Пришлось левый борт переоблицовывать на Сикафлексе. Правый борт до сих пор, 8 лет без проблем. Но на 6 году с целью уменьшения нагрева под лучами солнца окрасил стенки рубки в белый цвет.
Все наружные поверхности были облицованы на Сикафлексе. Опять же жесткое соблюдение технологии, рекомендованной производителем, имеет решающее значение для качественного результата. Для приклейки реек использовался Сикафлекс 292 с соответствующем праймером (грунтом). Для заполнения щелей палубной рейки Сикафлекс 290. О применении грунта есть интересное наблюдении. Когда облицовывал борт, остатки сикафлекса со шпателя смазывал на старую грязную краску металлического корпуса. В дальнейшем при механической очистке корпуса от краски оказалось, что сика держится на старой краске не хуже, чем на родном грунте. Также подобное наблюдал, когда наносил сику прямо на лакированные поверхности. Но это не значит, что можно отказаться от применения родного праймера, в данном случае Sika Primer-290DC, хотя желание такое появляется постоянно в силу его очень высокой цены.
Для заполнения зазоров палубной рейки использовался Sikaflex-290. Но палуба не из тиковой рейки, а из довольно редкого дерева Татаюба (иногда называют Татахуба). Поэтому лакировка палубы была необходимой. В тоже время производитель не дает гарантий на лакокрасочное покрытие, нанесенное на поверхность Сики. Конечно при лакировке палубы лак наносился сплошняком по рейке и по швам. Как говориться, производителю надо верить. Лак со швов конечно чулком не сходил, но за четыре месяца наблюдались трещины лака на швах. Лечилось многослойной лакировкой и весенними одним двумя слоями лака с предварительной легкой шлифовкой.


Для внутренней отделки применялся клей Беррит 303. Клей ПВА, но качество и свойства в разы лучше обычных ПВА клеев из хозмагов. При использовании без катализатора соответствует категории D3. Что такое D3 конкретно не интересовался, но по опыту можно считать влагостойким. При применении с катализатором обеспечивается категория D4. Опять же по опыту можно считать водостойким. Во всяком случае есть пример применения Беррит,а 303 с катализатором для наружной обшивки яхты, но под обклейку стеклопластиком. Следует иметь ввиду, что катализатор содержит цианиды, поэтому соблюдение производственной санитарии и техники безопасности лишним не будет.
Для примера образец китайского шпона, приклеенного на фанеру ФСФ клеем Беррит 303. Четыре года был верхней частью ящика над двигателем Д-65, поливало дождем, грело солнцем. Затем был вырезан этот кружек и лежал полтора года; весна, лето, осень, зима, весна, лето, и осень на улице под дождями и снегами.
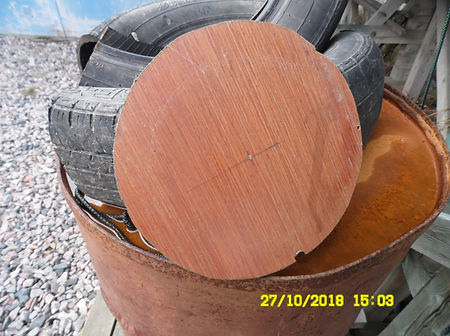

Применение силиконовых герметиков было эпизодическим, в местах ненагруженных, и как правило для обеспечения герметичности. Например по периметру фанерных переборок на стыке с обшивкой
ИЛЛЮМИНАТОРЫ И ОКНА. Установка, ответственный момент. Водотечность окон вещь неприятная, и как показала практика, трудноустранимая.
Но по порядку. Первое выбор стекла. Простое стекло, закаленное, триплекс из простого стекла, триплекс из закаленного. Применение простого стекла конечно не рассматривалось. Делать окна из закаленного тоже нехорошо, разлетится на мелкие осколки и сквозное отверстие в рубку обеспечено. Остановился на триплексе из обычного стекла, два стекла толщиной 4 мм. Второе - выбор способа крепления стекла. Решил ставить стекла на герметик, сикафлекс. Наименее трудоемко и не требуется изготовления каких-либо дополнительных деталей. Но к сожалению не нашел в 2010 году, кто бы мог сделать на стекла керамическое напыление, пришлось взамен слегка шлифовать привалочные плоскости. Стекла поставленные таким образом успешно прослужили шесть лет, позже стало видно, что герметик частично отходит от стекол. Особенно интенсивно на солнечной стороне. Пришлось по всем окнам ставить рамки из красного дерева. Рамки ставились на нейтральный силикон. Два года прошло, пока без проблем.


ОКРАСКА. Два раздела, окраска металлического корпуса и окраска (лакировка) деревянных деталей.
По окраске металлического корпуса возникает вопрос, а нужно ли красить алюминиевый корпус, точнее корпус из АМГ сплава. Конечно можно не красить, но внешний вид неокрашенного корпуса возрастом 60 лет не производит благоприятного впечатления. Поэтому красить однозначно.
Как и чем? И что поставить на первое место, окраску как защиту от коррозии, или окраску как составляющую экстерьера. Защита от коррозии для корпуса из АМГ не актуальна, разве только в местах, где присутствует возможность электрохимической коррозии, рядом с латунным гребным винтом и стальной мортирой гребного вала.
Чем красить, в смысле какими красками. Выбор широк. Дешевые алкидные с неплохими защитными свойствами, если конечно приобретать у проверенного продавца. Более дорогие эпоксидные, поли- и просто уретановые, и прочие экзотические отечественные и импортные. Остановился на алкидной краске Вика 60. Автомобильная ремонтная естественной сушки. Растворитель уайт-спирит. Недорогая. Правда производитель предлагает нанесение распылителем, что для меня по причинам, описанным ниже, не очень подходило. Но как показала практика, при соблюдении определенной технологии, нанесение кистью позволяет достигнуть хорошего результата. Еще один плюс в пользу алкидной однокомпонентной краски - ее более низкая трудоемкость ремонта по сравнению с многокомпонентными красками. Мне не трудно раз в два-три года подкрасить повреждения ЛК покрытия, не затрачивая много времени на подготовку.
Как красить, в смысле технологии и инструмента?
Способы окраски от лучшего к худшему в части защитных свойств ЛК покрытия, а не как *красивше*. Безвоздушное распыление, кисть, воздушное распыление, валик. Безвоздушка при моих минимасштабах отпала, осталась кисть. Но конечно по проверенной временем технологии, совсем не похожей на *Открыл банку, мокнул кисть и размазал*.
Теперь конкретика об окраске старого алюминиевого корпуса.
1. Зачистка от старой краски. От очень старой краски толщиной местами до 2 мм. Попытался использовать очиститель Б-52. Бесполезное занятие оказалось. Намазал половину квадратного метра, прикрыл пленкой, по краям скотч. На следующий день снялся только самый верхний тонкий слой. А ожидалось, что все 1-2 мм покрытия размягчится и легко снимутся при помощи шпателя. Пришлось снимать все краску, примерно 30 квадратных метров, механически. Болгаркой с лепестковыми кругами. Тяжелое занятие, особенно на днище. Средняя скорость 0,3 кв.метра в час. Выдерживал за день не больше 4 часов. Хорошо были помощники, хотя за ними следить надо было, а то бы все усиление сварных швов свели бы не нет.
2. Грунтовка ВЛ-02.Перед грунтовкой ручная зачистка шлифблоком. Соблюдение временных интервалов между зачисткой и нанесением грунта.
3. Окраска кистью. Краска разбавлялась уайт-спиритом почти до вязкости воды. Наносилось не менее 6 слоев с перерывом на просушку. Расход краски на один слой около 30 мл на 1 кв. метр. Краска тщательно растушевывалась. Визуальный показатель соблюдения технологии - окрашиваемая поверхность металла окончательно закрывается лишь шестым слоем краски.
Именно много тонких слоев обеспечивают качественное покрытие, которое в дальнейшем не полезет *чулком*.
Все эти три пункта были выполнены за два раза. Сначала надводный борт. Затем на следующий после спуска на воду год была зачищена и окрашена подводная часть.
Состояние ЛК покрытия надводного борта после восьми лет эксплуатации хорошее. За это время лишь один раз подновил надводный борт одним слоем жиденькой краски.
Краска Вика 60 показала себя прекрасно, не мелится. Солнце ее *не берет*. Сколов и шелушения не наблюдается.
Для подводной части Вика 60 конечно не подходит. Но для моего алюминиевого корпуса это не критично, хоть совсем не окрашивай, главное защитить в районе гребного винта.